Sharp Edge Coverage
Gleichmäßige Schutzlackierung von Leiterplatten
In der modernen Elektronikfertigung sind Schutzlacke (Conformal Coatings) auf Leiterplattenkomponenten ein unverzichtbares Mittel, um elektronische Baugruppen vor Umwelteinflüssen wie Feuchtigkeit, Staub, Chemikalien und Temperaturschwankungen zu schützen. Zum Einsatz kommen sie insbesondere in der Luft- und Raumfahrt sowie in der Militärtechnik oder der Automobilindustrie. Eine besondere Herausforderung stellt dabei die Beschichtung der scharfen Kanten von oberflächenmontierbaren Bauteilen dar, die sogenannte Sharp Edge Coverage (SEC): Unzureichend beschichtete Kanten können zu Bauteilausfällen und einer verkürzten Lebensdauer der Elektronik führen.
Dirk Rüdell und Nicolas Wiacker, Produktmanager für HumiSeal-Schutzlacke bei Stannol, beleuchten die technischen Herausforderungen von Sharp Edge Coverage bei Schutzlacken und stellen bewährte Verfahren und neue Technologien zur Gewährleistung einer vollständigen und gleichmäßigen Beschichtung vor.

Scharfe Kanten erschweren Beschichtung
Moderne Leiterplatten weisen heute komplexe Geometrien auf: zahlreiche scharfe Kanten und Übergänge sowie verringerte Abstände zwischen den Bauteilen bei gleichzeitig erhöhter Packungsdichte. Ungeschützte scharfe Kanten von Komponenten sind dabei besonders anfällig für Beschädigungen. Gleichzeitig erschweren sie den Auftrag einer ausreichenden Beschichtung, da Schutzlacke dazu neigen, sich an Kanten und Ecken ungleichmäßig abzusetzen.
Die Oberflächenspannung des Lacks kann zudem dazu führen, dass er sich von scharfen Kanten zurückzieht, was als „Edge Recession“ bekannt ist. An scharfen Kanten kann es daher leicht zu exponierten Bereichen kommen, die anfällig für Korrosion und elektrische Fehlfunktionen sind.
„Eine vollständige Abdeckung durch Schutzlacke ist entscheidend, um die Zuverlässigkeit und Langlebigkeit von sicherheitskritischen elektronischen Bauteilen zu gewährleisten. Eine gleichmäßige Beschichtung sorgt zudem für eine verbesserte elektrische Isolierung und verhindert Kurzschlüsse zwischen benachbarten Leiterbahnen oder Komponenten“, erklärt Dirk Rüdell.
Scharfe Kanten, die nicht vollständig beschichtet wurden, können zu einer Reihe potenzieller Fehler führen, zum Beispiel kann es in Kombination mit Kondensation auf der Leiterplattenoberfläche zu elektrochemischen Vorgängen oder Korrosion kommen. Dies kann Systemausfälle zur Folge haben.

Viskosität und Adhäsion entscheidend
Die physikalischen und chemischen Eigenschaften des verwendeten Schutzlacks beeinflussen maßgeblich die Fähigkeit zur vollständigen Abdeckung scharfer Kanten. Viskosität, Adhäsion und Aushärtungsmechanismen spielen dabei eine wichtige Rolle.
„Lacke mit zu geringer Viskosität können Probleme bei der Benetzung scharfer Kanten verursachen, da zu dünnflüssige Lacke dazu neigen, abzulaufen und unzureichende Schichten zu bilden. Eine hohe Viskosität hilft zwar bei der Benetzung scharfer Kanten, allerdings fließt der Schutzlack auf der ebenen Fläche der Leiterplatten schlechter, wodurch dort Ungleichmäßigkeiten entstehen können“, weiß Nicolas Wiacker.
Die Wahl des richtigen Schutzlacks ist deshalb entscheidend. „Lacke mit guten Benetzungseigenschaften und hoher Adhäsion sind besonders geeignet, um scharfe Kanten gleichmäßig zu beschichten. Spezielle Formulierungen, die eine bessere Fließeigenschaft und Oberflächenspannungskontrolle bieten, sollten bevorzugt werden“, betont HumiSeal-Experte Dirk Rüdell.
Sharp Edge Coverage mit nur einer Schutzlackschicht
Traditionell wird Sharp Edge Coverage durch das Auftragen mehrerer Schutzlackschichten erreicht, was ein zeitaufwändiger und kostspieliger Prozess sein kann. Zum Teil sind bis zu acht oder mehr Schichten nötig, um die gewünschte Schutzwirkung an den Kanten zu erreichen. Ziel ist dabei in der Regel die nach Norm IPC-A-610 vorgegebene Schichtdicke von 30 µm bis 125 µm.
Um die Deckkraft auf scharfkantigen Bauteilen zu erhöhen, hat Schutzlack-Hersteller HumiSeal zwei Produkte entwickelt, die eine vollständige Beschichtung in nur einem Anwendungsprozess ermöglichen: Die Schutzlacke 1B59 SEC und 1A33 SEC. Dadurch entfällt die Notwendigkeit, mehrere Lackschichten aufzutragen.
„Eine einzelne 80-µm-Schicht von 1B59SEC hat sich als wirksamer erwiesen als zwei oder mehr 40-µm-Schichten einer herkömmlichen Beschichtung, wie Tests von HumiSeal zeigen“, so Nicolas Wiacker.
Die SEC-Schutzlacke haben modifizierte Flüssigkeitseigenschaften, wodurch sie sich, insbesondere während der Trocknungsphase, besser an die Form der entsprechenden Komponenten anpassen können als klassische Schutzlacke.
Die SEC-Produkte bieten somit einen vollständigen Schutz für bestückte Leiterplatten – einschließlich der scharfen Kanten oberflächenmontierter Komponenten.
Immersionstest zeigt hohe Deckkraft
Um zu bestätigen, dass die neue Sharp-Edge-Coverage-Beschichtung den beabsichtigten Schutz bietet, wurde vom HumiSeal-Forschungslabor ein Immersionstest entwickelt. Bei diesem Test kommen ein Becherglas mit Salzwasser, dessen Salzgehalt dem von Meerwasser entspricht, eine 24-Volt-Stromversorgung und Testplatinen, die für die SIR-Bewertung und Kondensationstests entwickelt wurden, zum Einsatz.
Für den Test wurden zwei Testplatinen verwendet: eine Platine beschichtet mit einer einzelnen Schicht 1B59 SEC (80 µm) und eine Platine ohne Beschichtung. Die Testplatinen wurden dann an die Stromversorgung angeschlossen, mit 24 Volt bestromt und anschließend in das Salzwasser getaucht.
Das Ergebnis: Die unbeschichtete Platine zeigt eine deutliche Blasenbildung durch Leckstrom sowie eine schnell einsetzende Korrosion. Die mit 1B59 SEC beschichtete Testplatine weist hingegen keine Anzeichen von Leckstrom und Blasenbildung auf.
„Die SEC-Schutzlacke bieten vor allem zuverlässigen Schutz für Leiterplatten, die in hoher Luftfeuchtigkeit und rauen Umgebungen eingesetzt werden. Die Reduzierung der Schutzlackschichten führt zudem zu einer erheblichen Zeit- und Kostenersparnis “, so Dirk Rüdell.
HumiSeal SEC-Schutzlacke weisen folgende Vorteile auf:
- sehr gute Abdeckung von scharfkantigen Bauteilen
- äußerst geringe Wasserdampfdurchlässigkeit
- Schutz gegen Feuchtigkeit, salzhaltige/korrosive Umgebungen und Schmutz
- verbesserte thermische Stabilität im Vergleich zu anderen Schutzlacken
- fluoreszieren unter UV-Strahlung zur leichteren Inspektion
Fachliche Ansprechpartner
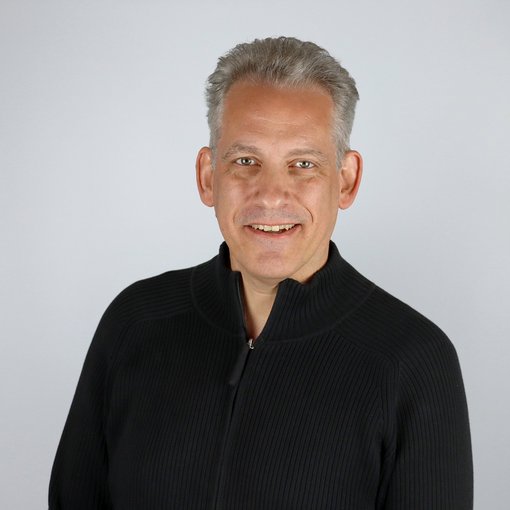
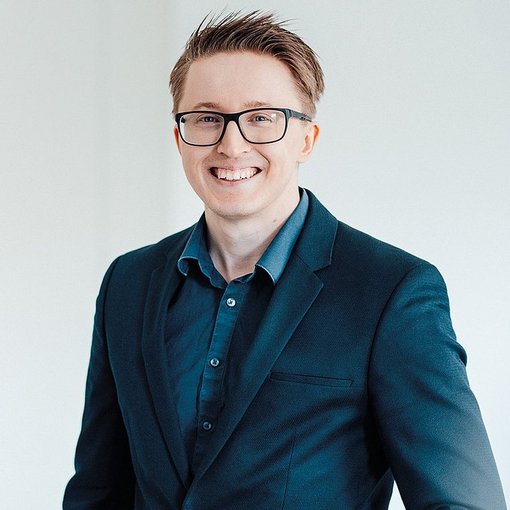
Autorin
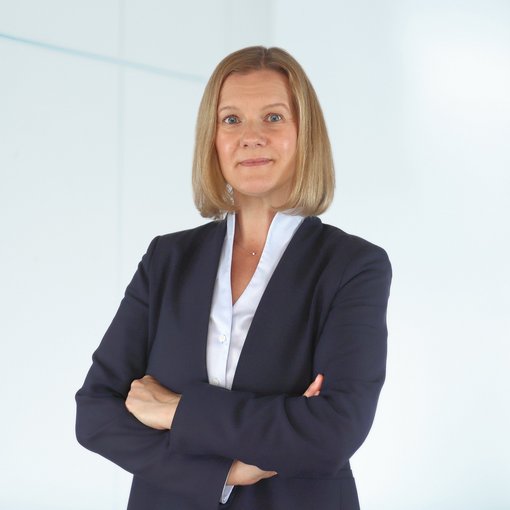