Sustainability Reporting For SMEs
A sustainable business approach is becoming increasingly important for medium-sized companies in order to achieve environmental, social and economic goals. The preparation of a sustainability report is therefore turning into an indispensable tool: the report creates transparency, informs stakeholders and discloses a company's sustainability performance. However, SMEs often lack the human resources to deal intensively with the topic.
In 2023, Stannol GmbH & Co KG published its first voluntary sustainability report according to the German Sustainability Code (DNK). Susanne Schlüter, Assistant to the Management and responsible for preparing the report, explains how the company proceeded and which challenges had to be overcome.
Identify your fields of action
Even if many SMEs are not yet legally obliged to report, there is a growing external pressure to take responsibility: Investors, customers, but also employees and other stakeholders are increasingly demanding transparent communication when it comes to the sustainable behaviour of companies. It is therefore worth addressing the issue at an early stage. "Stannol has long played a pioneering role in the soldering industry when it comes to sustainability. It therefore made sense for us to get to grips with the topic of sustainability reporting as soon as possible," explains Susanne Schlüter.
The first step is to gain an overview of the possible fields of action and to recognise key areas. "It is vital to concentrate on the essentials at the beginning, otherwise it quickly becomes confusing. You can also focus on things that are relatively simple to change, such as switching to green electricity," emphasises Schlüter.

Analysis of Significance
A significance analysis is recommended at the beginning to help identify your own areas of action. The upstream and downstream supply chains also play a role here. In the case of Stannol, there are opportunities to influence Scope 3 emissions in the upstream supply chain in particular.
‘The analysis has shown that most of our emissions are caused by the way we source metals and chemicals. This means that we have the greatest potential for reducing emissions when purchasing goods from this area. For other companies, however, the focus can also be on transport, waste management or travel costs, for example,’ explains Schlüter.
Once the main areas of action are known, a strategy can then be defined with the aim of reducing emissions primarily in this particular field. To achieve this, it is also important to engage in dialogue with all departments in the company. Here, individual focal points can be identified and specific departmental goals and measures can be defined. These can then be gradually expanded.
Energy Efficiency Consulting
In general, you should also take a look at the emissions emitted directly by the company (Scope 1 and 2) and check electricity, water and gas consumption, for example. To achieve this, Stannol took advantage of an energy efficiency consultation, which is supported by subsidies. Following the consultation, short, medium and long-term measures were identified and initiated directly, for example installing energy-saving LEDs, equipping radiators with smart thermostats, retrofitting boilers and installing insulating slatted curtains on the gates of the production hall. In addition, ceiling fans are now used in production to improve heat distribution.
Water consumption has also been drastically reduced with the help of flow meters. Susanne Schlüter: ‘Compared to the metals, all our other consumption is rather low. Nevertheless, measures are also important here. If you take care of energy-saving measures within the company, you set an example. It creates awareness among employees and encourages them to contribute their own ideas.’
Data Availability Proves Problematic
Once the fields of action have been determined, valid key figures must first be collected and defined. This is not only important to determine the status quo, but also to achieve reliable comparability in the future. "Initially, we had a lot of work to do with collecting key figures such as consumption data, as well as detailed order quantities of primary and secondary tin and data from the personnel area. These figures were not consistently documented until now. However, it is worth investing time here so that the data basis is also available on a long-term and valid basis. Data collection is now well established in all departments," explains Susanne Schlüter. The biggest change in strategy was initiated in the purchasing department: By switching to almost exclusively recycled and fair trade tin, most emissions have been saved.
Sustainability As A Corporate Strategy
A further problem, especially for smaller companies, is the need to manage responsibilities when personnel resources are often already scarce. However, sustainability reporting requires a lot of time, especially at the beginning, for example for research and internal data collection. At Stannol, the management team has addressed the issue - in addition to their actual duties. ‘We wanted to emphasise that the topic is a priority for us and is closely linked to the strategic direction of the company. For us, this was essential in order to be perceived as acting authentically and holistically,’ emphasises Schlüter.
Exchange And Networking
The company was supported in the preparation of the report by student assistants from relevant departments. They were not only able to take on many tasks, but could also provide helpful input thanks to their young, sustainable perspective from the outside. Further training, exchanges in forums and constant dialogue with other companies from the region and players from the industry were also helpful in preparing the report. "Asking lots of questions, learning from others and developing solutions together – that has helped us move forward. You should also have the courage to leave gaps. Not everything has to be complete right from the start. The important thing is to get started, keep at it and document the areas where there are still deficits so that you can continue to work on them," explains Susanne Schlüter.

Motivating Colleagues
One of the biggest challenges was to raise awareness regarding the issue of sustainability in the individual departments. "It's important to get the employees on board and involved. Intrinsic action based on personal conviction is ideal – but this is a long process. However, a lot can be achieved by showing colleagues their own areas of action and opportunities for involvement," explains Susanne Schlüter.
A sustainability circle, consisting of interested employees from all departments, serves as a platform at Stannol to contribute their own ideas. Also important: each department should try to get into dialogue with the respective stakeholders on the topic of sustainability – sales with the customers and purchasing with the suppliers.
"We want to try to get other stakeholders on board as well in order to maximise the overall impact. We want to be a role model – for our employees, the industry and within the supply chain," says Schlüter.
Key Figures From Databases
The lack of emission data in public databases proved to be a fundamental challenge. Stannol uses many raw materials, the data of which first had to be determined individually. However, no data is available for many chemicals and resins, for example. These had to be researched at great expense. "Missing data is a major problem for valid calculations. However, the quality of the databases is improving as demand continues to grow. This will make it easier to access reliable and comprehensive emissions data in the future," Susanne Schlüter is certain.

The Next Steps
Stannol will publish the second Sustainability Report for the 2023 reporting year in the summer. Many measures have been initiated, so a comparison with the previous year is worthwhile: "The figures clearly show that medium-sized companies can have a major influence on their emissions – and are also responsible for them," emphasises Schlüter.
But Stannol is also making progress in other areas: since the beginning of 2024, the company has been reporting the product carbon footprint (PCF) for over 1,600 of the goods it manufactures itself. "This means that our customers can now see exactly how much CO2 a product has caused. This makes it easier to compare – and to decide in favour of a more sustainable product." In spring, Stannol also renaturalised around 1,000 m2 of land in the outdoor area, which had been sealed with concrete and remained unused for over twenty years. There are also plans to install a PV system and a water cooling circuit.
Contact our Expert
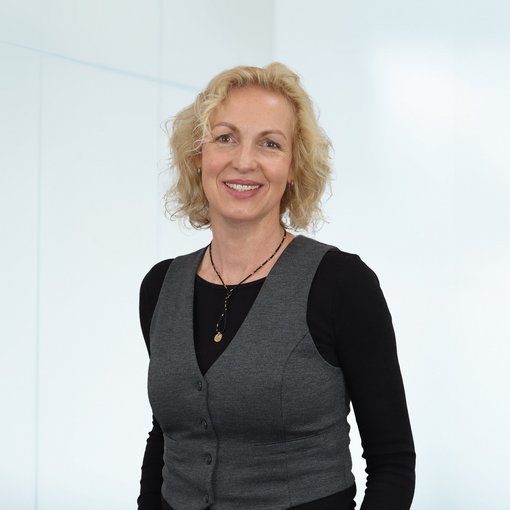
Author
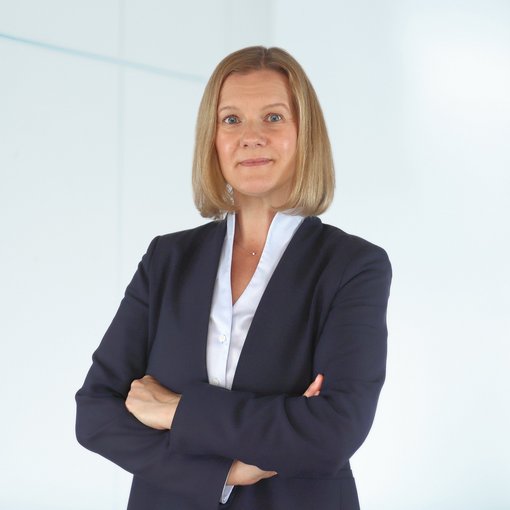