Change in IPC: Objective Evidence through SIR Testing
In the American standard IPC J-STD-001, the basic standard for electronics manufacturing, there has been a change around the detection of ionic residues on process materials in 2020. In the current revision H (09/2020) of the standard, it was specified that the safety of ionic residues must now be demonstrated by so-called "objective evidence".
Prior to the current revision, the standard only required the ROSE test to determine ionic residues on printed circuit boards. ROSE stands for "Resistivity Of Solvent Extract", i.e. the resistance of a solvent extract of the residues. In this test, the limit of 1.56 µg/cm² NaCl equivalent could not be exceeded. This means that 1.56 micrograms equivalent of common salt per square centimeter of the printed circuit board was permissible. The problem: The limit value for the ROSE test was established about fifty years ago and laid down in the standard. A lot has happened in the electronics industry since then. Different processes, a variety of materials and ever increasing miniaturisation are only the most important changes.
As a result, this limit value no longer meets the complex requirements of the electronics industry. In addition, the value is not very meaningful when it comes to the actual risk of electrochemical migration on printed circuit boards. "The limit value was generally defined and applied regardless of the assembly, the conditions of the subsequent place of use or the packing density. However, taking these parameters into account individually is important for assessing the cleanliness of PCBs or the safety of ionic residues," explains Nicolas Wiacker, Product Manager at Stannol.
What is "Objective Evidence"?
The amendment to the standard took an important step toward measurable safety by now requiring individual objective evidence of ionic residue safety. "Objective evidence includes that electronic assemblies must be clean enough to function reliably during their expected lifetime and intended climatic conditions of use. There is no longer a general fixed limit," Wiacker emphasises. What "clean enough" means depends on the individual assembly and its area of application and must be determined separately for each manufacturing process.
SIR test as a simulated manufacturing process
Objective Evidence can be achieved primarily through SIR tests, in which the test structures used must pass through the entire production cycle, including all the process materials used. This means that the process itself, the equipment used and all materials such as solder pastes, fluxes and conformal coatings must be included in the consideration. "If the SIR test is passed under these conditions, the standard is fulfilled with regard to the required objective evidence," says Wiacker. In this context, the test structure must represent the assembly under test as closely as possible to production – for example, in terms of the components used and the distances between the conductive tracks. As standard, the SIR test according to IPC J-STD-004C requires 168 hours, during which a surface insulation resistance of 108 ohms must not be fallen short of. For particularly safety-critical elements, such as in the field of e-automobiles, the test duration is often extended to over 1,000 hours as part of "end of life" tests.
Equipment for determining the objective evidence
SIR test procedure
To determine the electrical safety of fluxes in soldering technology, the surface insulation resistance (SIR) must be measured. Specifically, this involves determining the insulation resistance between adjacent conductors on the surface of a printed circuit board. The IPC J-STD-004C standard requires a resistance of at least 108 ohms, which must be maintained over a period of 168 hours. Meanwhile, a kind of worst-case scenario is created: The prepared circuit boards are energised in a climatic cabinet at 40 degrees Celsius and 90 percent relative humidity.
New test required for process changes
In order to check the cleanliness of the printed circuit board after the SIR test has been passed, a ROSE test is also carried out afterwards. The result is again the basis for a new limit value, which can then be set specifically for this individual manufacturing process. The value obtained can be higher or lower than the old limit of 1.56 µg/cm² NaCl equivalent – depending on the application of the assembly. "As soon as changes are made in the process, for example if components, solder pastes, fluxes or conformal coatings are replaced, the temperature profile changes significantly or the system is relocated to another, external site, the objective proof according to the standard must be provided again and the test repeated," the expert emphasises.
Ion chromatography for the qualitative determination of residues
As an alternative to determining objective evidence, ion chromatography can also be considered. In this case, the ionic residues on the assembly under test are dissolved in a liquid and identified by ion chromatography. The difference to the SIR test is that ion chromatography detects qualitative impurities, while the SIR test targets quantitative impurities. Nicolas Wiacker: "In principle, an SIR test is well suited for determining objective evidence. However, ion chromatography can make sense if there are problems with the SIR test, for example, if the test is not passed. Ion chromatography can then be used to check which impurities are actually present. It may then be possible to draw conclusions about the source of the residues so that they can be eliminated."
Testing: internal or external
SIR measurements are complex: The tests must be carefully prepared and carried out over a long period of time. The pure running time of an SIR test in the climatic chamber is at least 168 hours, but often several weeks. In addition, there is the complex preparation of the test structures, which first have to be reproduced close to the process. Whether the tests are performed internally or externally depends, among other things, on the quantity of tests required. Both have advantages and disadvantages: "With internal tests, there are first of all high investment costs for the test equipment. In addition, you need experienced and well-trained specialists who can reliably perform the test. At the same time, however, you can adapt processes or repeat tests more quickly and have full control over the tests – without having to pass on internal information to third parties," explains Nicolas Wiacker.
External laboratories offer the advantage that experienced users are responsible for the tests. Disadvantages can be that one is less flexible and logistics must also be taken into account: During transport or longer storage, the sensitive test structures can quickly be damaged or contaminated. The cost of an external laboratory depends on the number of structures to be tested. Nicolas Wiacker: "Larger companies with many or frequently changing processes should consider internal testing, while for smaller companies external testing is often more appropriate for cost reasons."
Contact our Expert
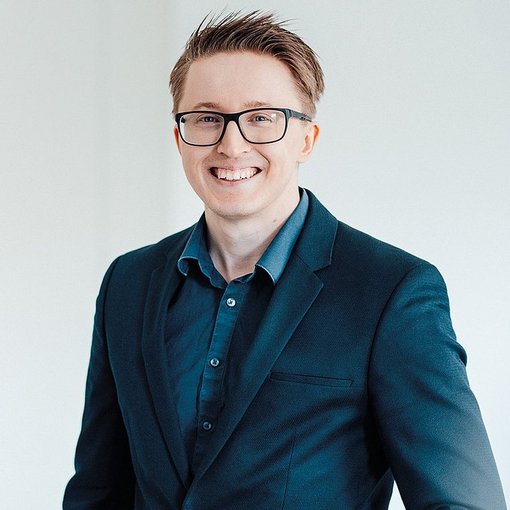
Nicolas Wiacker
Technical Sales, Measuring & Testing Systems, HumiSeal
Email nicolas.wiacker@stannol.de
Author
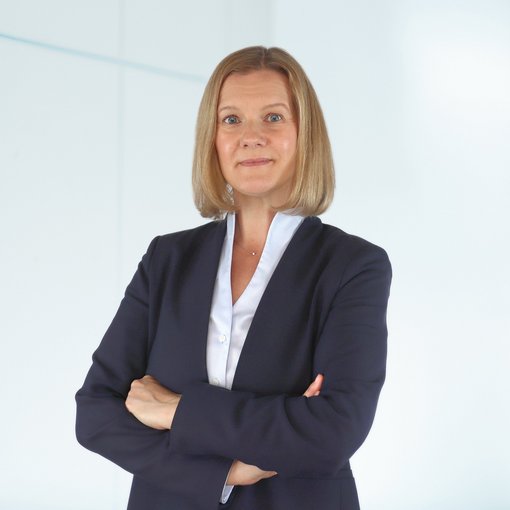